Brief summary
The pipe extrusion process is critical for manufacturing various piping systems essential to modern infrastructure. In the article below you will discover the stages of pipe production, from extruding raw plastic into a tubular shape to cooling, cutting, or coiling the finished product. This is also a in-depth analysis of different extrusion techniques and equipment, emphasizing the importance of precise calibration and cooling methods to ensure product quality
In Europe there are more than 550 manufacturers of piping system
This is a sector which has much relevance. And pipes are without doubt indispensable components in many of the infrastructures that surround us. The pipe extrusion is in fact the topic of this article.
A pipe extrusion line consists of different parts. An extruder converts raw plastic material into a continuous tubular melt by extrusion through an annular die. The molten pipe then proceeds through a sizing or calibration bench (which adjust its dimensions) to a cooling tank. After being cooled, the pipe passes via an haul-off to the cutting machine, for cutting it into final lengths, or coiling.
Single or Twin screw extruders are used for pipe manufacturing.
Extrusion Process
The profile or tube are pulled by an haul-off unit so that the line it is always in motion. Finally, depending on the flexibility of the product, a cutting or winding unit prepares the product for distribution.
In the head there is much of the secret of a good product. It can be a model with porta mandril, with spiral, or with lateral feed. Each of these designs provides a different flow.
The calibration bench, if we talk about pipelines, has the function of providing to the pipe a specific diameter and the circular shape that the product requires. You can do the calibration using vacuum or pressure.
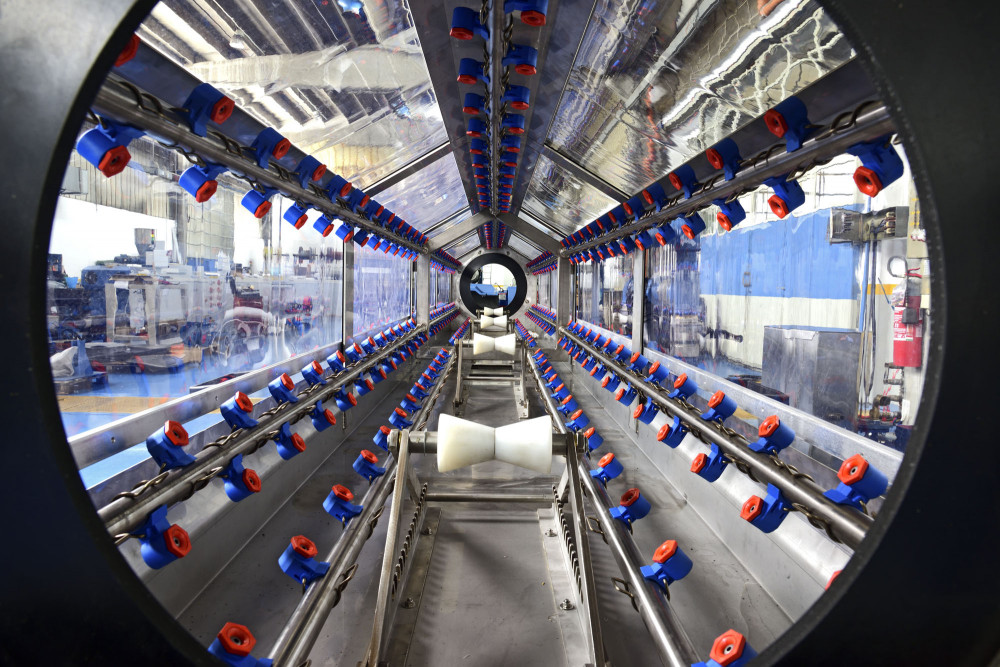
* Pipe Cooling System
For smooth pipes the most common system is the vacuum calibration. The vacuum caused on the outside of the tube allow the polymer, yet malleable thanks to the high temperature, stay in contact with the metal pipe head which has an inside diameter equal to the outer diameter specific for the product.
In the case of corrugated pipes, vacuum calibration use the same principles as for the smooth tube. In the calibration of the corrugated pipe, the pressurized air penetrates through the channels practiced in the head and they inject the material in the still hot extruded tube. The difference in pressure caused, shapes the surface of the plastic pipe pushing it against the system, providing the product the required corrugation.
The cooling phase
And then, we got to the cooling tank that eliminates the residual heat of the pipe that remains at the exit of the calibration tank. The importance of cooling, lies in the stability that acquires the plastic to not deform when passing through the haul off unit, where the tube is subject to pressures that could produce alterations in the circular shape required.
By spray or immersion baths you can cool it down. The first system is used for pipes with large diameter, where production speeds are low and the spray can achieve effective cooling. In the immersion the tube passes through a water-filled container in constant cooling.
Once cooled, it pass to the Haul off unit, which generates all the strength which, to put it in some way, pulls the profile or tube in order to extract it from the extrusion line.
The final cutting
The last step is the cutting unit, which also depends on much of the type of product that is manufactured. If we talk about pipe and the pipe is coiled, the cut is logically a little relevant work. But many tubes should be cut out of the extruder in equal lengths, either by lack of flexibility to be coiled or other considerations. When choosing the cutting system must be taken into account the diameter and wall thickness, the raw material used, the shape, quality and the length of the cut.
Cutting by guillotine is effective, but can produce slight deformations by the impact of the blade. With saw cuts the small dentures that cut the pipe cause small shavings that sometimes remain attached to the tube.
To avoid the formation of these residues, it is used a mechanisms where the blades are inserted in the wall of the tube and spin at high speed, producing only a strip of shavings but preventing deformations.
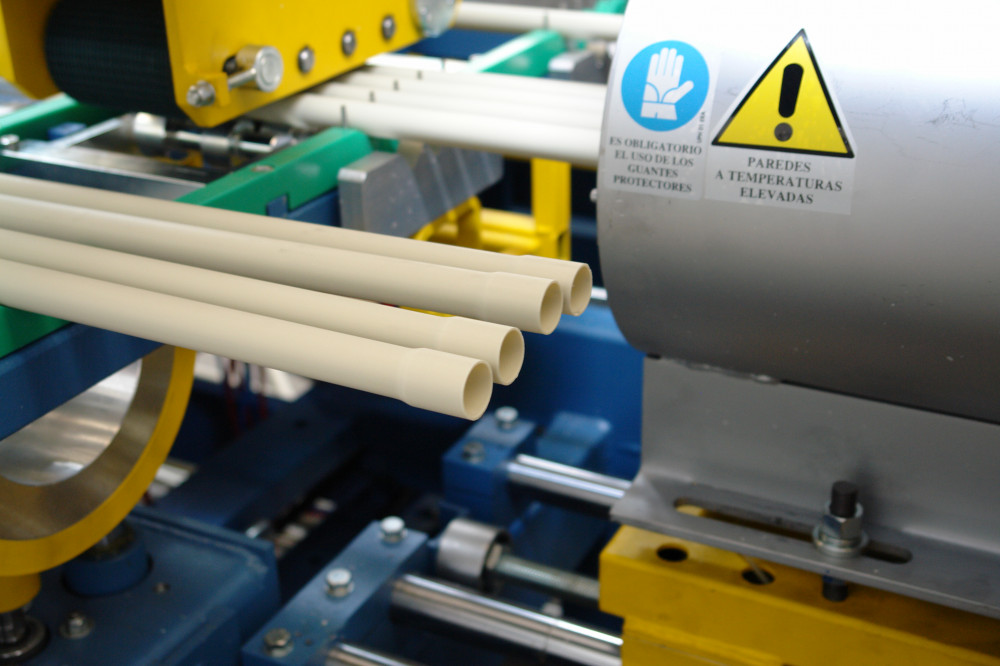
*Pipe Belling Machine