In Brief
Co-extrusion is a process that forms a multi-layer system using different materials, with polymer viscosity ensuring the layers remain distinct. It requires precise control of pressure and temperature to maintain optimal flow. In the following article, we’ll dive deeper into how this process works and explore its key advantages.
What is plastic co-extrusion?
Co-extrusion is a process in which multiple materials are extruded together to create a multi-layer system. Each material comes from a different extruder and is organized into layers when passing through the die. The process relies on the viscosity of the polymers to prevent mixing and ensure even distribution of one material over another.
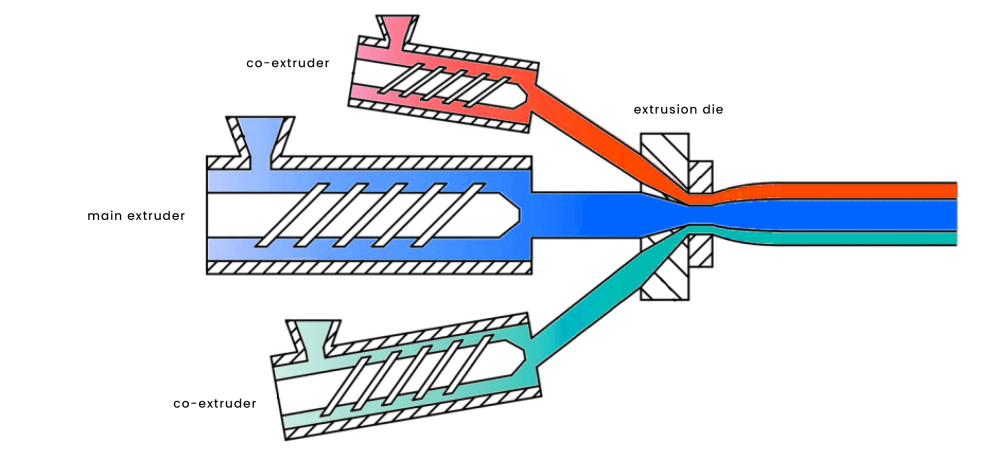
What is the process of co-extrusion?
Just like with simple extrusion, the polymers must be plasticized and flow without degradation, requiring precise control of pressure and temperature. Additionally, the residence time of the material in the barrel must be minimized to avoid damage.
-
Structure of Co-extruded products
The co-extruded product’s structure consists of multiple layers, each bringing different properties, such as thermal resistance, moisture and oxygen barriers, mechanical strength, and aesthetic qualities. Co-extrusion allows combining these properties in a single component, often leading to cost savings and enhanced performance.
Critical issues during co-extrusion can include the mixing or instability of the layers, often caused by the viscosity mismatch between polymers. If the flow isn't laminar or the polymers don't combine at the correct temperature and pressure, defects like zigzagging or encapsulation can occur, leading to compromised products. Variations in melt temperature and incorrect system designs can further exacerbate these problems, affecting the uniformity and quality of the layers.
What are the advantages of co-extrusion?
Co-extrusion offers numerous advantages, including the ability to produce high-performance components for various industries. It allows for the creation of products with distinct properties, such as thermal, moisture, and oxygen resistance. Additionally, the process enables significant cost savings by incorporating recycled materials into non-surface layers, while more expensive or functionalized materials are limited to the outer layers. Co-extrusion also allows the production of components with varying rigidity, which can be used across industries like construction, food, and automotive, with cost-effective and long-lasting results.
Disadvantages of co-extrusion
Some of the key challenges in co-extrusion include managing the viscosity difference between materials and ensuring laminar flow. Instabilities at the interface between layers can lead to distortion and decoupling of the polymer flows, negatively impacting product quality. When the viscosity mismatch is too high, issues such as phase mixing and encapsulation of one material by another can occur, causing irregular thickness or defects in the final product. Proper system design and control of temperature and pressure are essential to avoid degradation and other quality issues.
Applications
Co-extrusion is often used in the blow molding process for creating large plastic parts with multiple layers, such as automotive fuel tanks, where different layers contribute specific properties like fuel resistance or structural integrity.
-
Pipe and tubing applications
In the construction sector, co-extrusion is widely used for producing pipes and tubes. Success in these applications depends heavily on material selection and ensuring that the layers flow together with proper thickness ratios and laminar motion. Degradation or incorrect temperature settings can cause defects like discoloration or ovalization of the pipe.
Co-extrusion is also employed in the production of technical profiles, where different materials can be combined to achieve specific properties such as rigidity, flexibility, or aesthetic appeal.
For wires, co-extrusion is used to apply functional layers like insulation or colored strips, combining multiple materials to improve electrical performance and durability.
Differences Between Co-Extrusion and Traditional Extrusion
Co-extrusion and traditional extrusion differ significantly in terms of process complexity and product capability. While traditional extrusion uses a single material to create uniform products, co-extrusion allows the combination of multiple materials in distinct layers within the same product. This multi-layered approach opens up opportunities for greater customization
-
Multi-material Capability
In traditional extrusion, only one material is used, which limits the functionality of the final product. Co-extrusion, on the other hand, enables the simultaneous use of different polymers, each bringing unique characteristics, such as flexibility, rigidity, or resistance to moisture and heat. This allows manufacturers to design products with tailored properties for specific applications.
-
Complex Product Structures
Co-extrusion enables the creation of more complex structures by layering materials with distinct functions, such as barriers or reinforcement, resulting in products that outperform single-material components.
Co-extrusion offers far more flexibility in product design than traditional extrusion. Manufacturers can control the thickness, material composition, and placement of each layer to meet specific performance requirements. This level of customization is especially valuable in industries like automotive, packaging, and construction, where different parts of a product may need different properties, such as enhanced durability or chemical resistance.
Materials in Co-extrusion
Co-extrusion involves processing a wide variety of thermoplastic materials, each chosen for its specific properties that contribute to the final product. Here are some of the most important materials used in co-extrusion:
-
PVC (Polyvinyl Chloride):
One of the most versatile and widely used thermoplastics in co-extrusion. PVC is valued for its excellent durability, chemical resistance, and cost-effectiveness. It's commonly used in pipes, medical tubing, and profiles for the construction industry.
-
PE (Polyethylene):
PE is known for its flexibility, impact resistance, and moisture barrier properties, making it ideal for applications like packaging films, tubing, and wire coatings. It is often co-extruded with other materials to enhance moisture resistance.
-
PP (Polypropylene):
With a good balance of stiffness, strength, and chemical resistance, PP is frequently used in automotive parts, medical devices, and packaging. Its thermal stability makes it a popular choice for products exposed to higher temperatures.
-
PC (Polycarbonate):
Polycarbonate is prized for its impact resistance and transparency, making it ideal for applications requiring toughness and optical clarity. It is commonly used in the production of technical profiles, panels, and sheets for construction and electronic components.
-
PA (Polyamide or Nylon):
Polyamide offers high mechanical strength and wear resistance, often used in automotive parts, gears, and industrial applications. It also has excellent resistance to abrasion and chemicals, which makes it valuable in technical profiles and tubing.
-
PMMA (Polymethyl Methacrylate):
Known for its clarity and scratch resistance, PMMA is often used as an alternative to glass. Its optical properties make it ideal for lenses, lighting covers, and transparent sheets.
-
PEEK (Polyether Ether Ketone):
PEEK is a high-performance thermoplastic used in demanding applications due to its exceptional mechanical properties, chemical resistance, and heat tolerance. It is commonly used in aerospace, automotive, and medical industries, especially for components that require strength and durability under extreme conditions.
-
FEP (Fluorinated Ethylene Propylene):
FEP provides excellent non-stick properties and chemical resistance, often used in coatings, tubing, and wire insulation. Its ability to maintain performance across a wide temperature range makes it ideal for harsh environments.
Each material can be strategically placed in a specific layer during co-extrusion to optimize the final product’s performance, whether it’s for mechanical strength, insulation, or aesthetic quality. By leveraging the properties of these materials, manufacturers can create advanced, multi-functional products suitable for a wide range of industries.
Bausano's co-extruding solution
Bausano provides a comprehensive range of co-extruders used in industries such as medical, research, and plastics manufacturing. Our co-extruders are capable of processing a wide range of thermoplastic materials and are used for producing medical tubes, multilumen tubes, co-extruded tubes, technical profiles, plates, sheets, and co-extruded colored strips on tubes, cables, and profiles. Bausano’s focus on controlling polymer viscosity ensures high-quality products and minimizes issues related to interface instability and material mismatch.