Bausano presents its innovative vent designs for single-screw extruders. By exploring the unique challenges and solutions in vent design, including the importance of polymer viscosity and flow dynamics, Bausano demonstrates their commitment to innovation and superior engineering in constantly enhancing extruder performance.
Bausano single-screw extruder vent design
Bausano manufactures high-performance, customised single-screw extruders to meet any needs. From the very beginning, we have ensured the highest standards, been constantly open and keen to improve and stay up to date with advances in the industry, always with a focus on the future. For Bausano, air vent design for screw extruders is an important aspect, which we will look at more closely here.
The Extruder Design Process
The starting point to properly design a vented screw for a single-screw extruder is to understand how Bausano’s extruder vents can work for the devolatilization of polymers. The process starts with the first metering section, which is filled with polymer (I), and as it reaches the vent section (II), the channel volume increases. This eliminates any pressure in that area and clears an open space. A deflector must be placed in the barrel opening to avoid any vent flow that would clog the hole to atmosphere or vacuum. This means that the deflector design is critical, because without it, no screw design will vent properly.
The deflector is configured so that the amount of polymer that squeezes out as the screw flight passes the vent opening (III) will be scraped off and accumulate in the relief area. The amount must be small enough to fill only a portion of the relief area, without pushing any polymer back into the vent hole. The amount left in the relief area is pushed out by the next flight and refilled. If the relief is the right size for the amount being scraped off, the vent to atmosphere stays open and it becomes a steady-state process allowing volatiles to exit.
Proper vent design requires the right knowledge of polymer flow in the screw channels.
The molten polymer is attached to both the screw and the barrel, and from the perspective of a stationary screw, the motion of the polymer in the channel is equal to the rotational speed of the barrel on the barrel wall and zero at the root of the screw (Fig. 2). Across the channel depth, the polymer is transported forwards by the combination of the rotating shear stress and the angle of the screw flight.
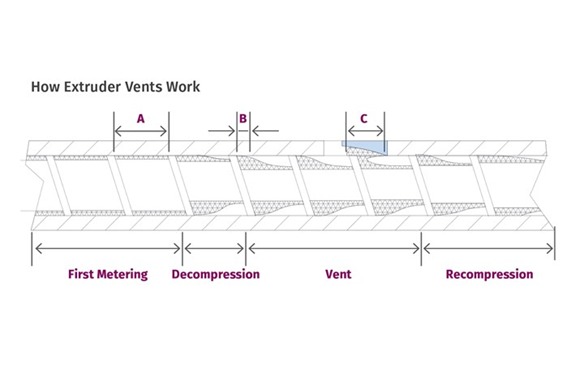
Vent design: how extruder vents work
It is fundamental to take into account the polymer viscosity because it affects the achievement of the exact 3D shape of the shear stress and its resultant velocity.
The lower the viscosity, the more the polymer “sags”, causing the barrel contact area to become narrower, and the shear-stress level deteriorates more rapidly approaching the root of the screw. This has a negative effect on the flow rate in the vent.
A proper vent design requires knowledge of the viscosity at the shear rate and melt temperature of the polymer in the vent. The forward transport or output is then a combination of the angle on the flight or scraper and the viscosity and the amount of polymer in contact with the barrel wall (B). This is unlike the full channel, where the entire channel width contributes to forwarding.
In the decompression section, the amount of polymer in contact with the barrel wall decreases but this decrease has to be compensated by increasing the volume in the channel. Channel depth can have little to do with the amount of forwarding as it is controlled by the diameter of the polymer in contact with the barrel wall, as well as the viscosity.
Vent design: understanding polymer flow in screw channels
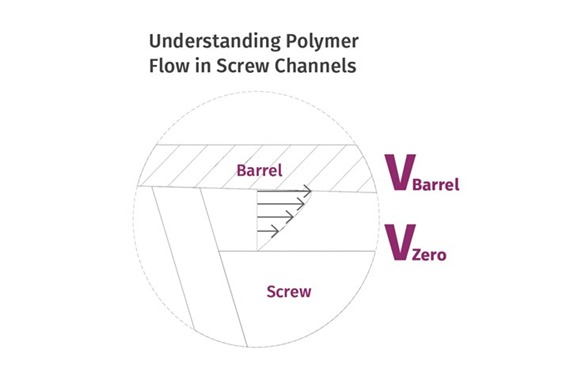
When it comes to decompression sections, it is common in screw design to simply use a ratio to the first metering depth for the air vent design, which is typically between 2:1 and 3:1 of the first metering depth. Air vent design is very important for high-melt-flow polymers because the shear stress deteriorates more quickly, reducing the mass flow.
To improve devolatilisation with more surface renewal, there are numerous designs with multiple flights available. These show an increase in the flight pitch in the vent, based on the idea that this technique gives more space for proper devolatilisation. Longer pitch improves surface exposure but there are drawbacks to this. Multiple flights take up more space, not allowing enough separation between the bank and barrel wall (II) to permit good venting. To compensate, these designs can use deeper channels or longer flight pitch to allow for more open space in the vent, but longer pitch makes it extremely sensitive to even the slightest head pressure.
Also, when using multiple flights, special features must be included at the inlet to the vent that will allow all the channels to fill evenly or you will have intermittent vent flow.