En bref
La coextrusion est un procédé qui permet de former un système multicouche à partir de différents matériaux, la viscosité du polymère garantissant que les couches restent distinctes. Elle nécessite un contrôle précis de la pression et de la température pour maintenir un flux optimal. Dans l'article suivant, nous allons approfondir le fonctionnement de ce procédé et explorer ses principaux avantages.
Qu'est-ce que la co-extrusion plastique ?
La co-extrusion est un processus dans lequel plusieurs matériaux sont extrudés ensemble pour créer un système multicouche. Chaque matériau provient d'un extrudeur différent et s'organise en couches lorsqu'il passe par la filière. Le processus repose sur la viscosité des polymères pour éviter le mélange et garantir une distribution uniforme d'un matériau sur l'autre.
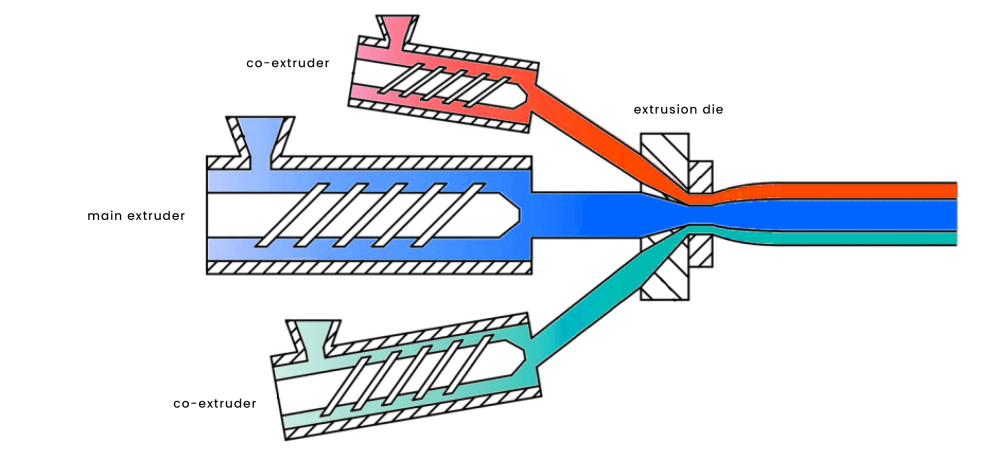
Quel est le processus de co-extrusion ?
Tout comme pour l'extrusion simple, les polymères doivent être plastifiés et s'écouler sans se dégrader, nécessitant un contrôle précis de la pression et de la température. De plus, le temps de séjour du matériau dans le cylindre doit être minimisé pour éviter tout dommage.
-
Structure des produits co-extrudés
La structure du produit co-extrudé se compose de plusieurs couches, chacune apportant des propriétés différentes, telles que la résistance thermique, des barrières contre l'humidité et l'oxygène, la résistance mécanique et des qualités esthétiques. La co-extrusion permet de combiner ces propriétés dans un seul composant, souvent entraînant des économies de coûts et une performance accrue.
Les problèmes critiques lors de la co-extrusion peuvent inclure le mélange ou l'instabilité des couches, souvent causés par une différence de viscosité entre les polymères. Si le flux n'est pas laminaire ou si les polymères ne se combinent pas à la température et à la pression adéquates, des défauts tels que des zigzags ou l'encapsulation peuvent se produire, compromettant ainsi les produits. Les variations de température de fusion et les conceptions incorrectes du système peuvent aggraver ces problèmes, affectant l'uniformité et la qualité des couches.
Quels sont les avantages de la co-extrusion ?
La co-extrusion offre de nombreux avantages, notamment la possibilité de produire des composants haute performance pour diverses industries. Elle permet la création de produits aux propriétés distinctes, telles que la résistance thermique, à l'humidité et à l'oxygène. De plus, le processus permet des économies de coûts importantes en incorporant des matériaux recyclés dans les couches internes, tandis que des matériaux plus coûteux ou fonctionnalisés sont limités aux couches externes. La co-extrusion permet également la production de composants avec une rigidité variable, pouvant être utilisés dans des secteurs tels que la construction, l'alimentaire et l'automobile, avec des résultats économiques et durables.
Inconvénients de la co-extrusion
Les principaux défis de la co-extrusion incluent la gestion de la différence de viscosité entre les matériaux et l'assurance d'un flux laminaire. Les instabilités à l'interface entre les couches peuvent entraîner une distorsion et un découplage des flux polymères, impactant négativement la qualité du produit. Lorsque la différence de viscosité est trop importante, des problèmes comme le mélange de phases et l'encapsulation d'un matériau par un autre peuvent survenir, entraînant une épaisseur irrégulière ou des défauts dans le produit final. Un bon design du système et un contrôle adéquat de la température et de la pression sont essentiels pour éviter la dégradation et d'autres problèmes de qualité.
Applications
-
Moulage par soufflage de grandes pièces
La co-extrusion est souvent utilisée dans le processus de moulage par soufflage pour créer de grandes pièces plastiques avec plusieurs couches, telles que les réservoirs de carburant automobile, où différentes couches apportent des propriétés spécifiques comme la résistance au carburant ou l'intégrité structurelle.
-
Applications de tuyaux et tubes
Dans le secteur de la construction, la co-extrusion est largement utilisée pour la production de tuyaux et de tubes. Le succès dans ces applications dépend fortement de la sélection des matériaux et de l’assurance que les couches s’écoulent ensemble avec des ratios d'épaisseur appropriés et un mouvement laminaire. La dégradation ou des réglages incorrects de température peuvent entraîner des défauts tels que la décoloration ou l’ovalisation du tuyau.
La co-extrusion est également employée dans la production de profilés techniques, où différents matériaux peuvent être combinés pour obtenir des propriétés spécifiques, telles que la rigidité, la flexibilité ou l'attrait esthétique.
Pour les câbles, la co-extrusion est utilisée pour appliquer des couches fonctionnelles comme l’isolation ou des bandes colorées, combinant plusieurs matériaux pour améliorer la performance électrique et la durabilité.
Différences entre la co-extrusion et l'extrusion traditionnelle
La co-extrusion et l'extrusion traditionnelle diffèrent significativement en termes de complexité de processus et de capacité produit. Alors que l'extrusion traditionnelle utilise un seul matériau pour créer des produits uniformes, la co-extrusion permet la combinaison de plusieurs matériaux en couches distinctes au sein d'un même produit. Cette approche multicouche ouvre des opportunités pour une plus grande personnalisation.
Dans l'extrusion traditionnelle, un seul matériau est utilisé, ce qui limite la fonctionnalité du produit final. La co-extrusion, en revanche, permet l'utilisation simultanée de différents polymères, chacun apportant des caractéristiques uniques, telles que la flexibilité, la rigidité ou la résistance à l'humidité et à la chaleur. Cela permet aux fabricants de concevoir des produits avec des propriétés personnalisées pour des applications spécifiques.
-
Structures de produits complexes
La co-extrusion permet la création de structures plus complexes en superposant des matériaux avec des fonctions distinctes, comme des barrières ou des renforts, aboutissant à des produits qui surpassent les composants à matériau unique.
La co-extrusion offre une flexibilité bien plus grande dans la conception des produits que l'extrusion traditionnelle. Les fabricants peuvent contrôler l'épaisseur, la composition du matériau et l'emplacement de chaque couche pour répondre à des exigences de performance spécifiques. Ce niveau de personnalisation est particulièrement précieux dans des industries telles que l'automobile, l'emballage et la construction, où différentes parties d'un produit peuvent nécessiter des propriétés différentes, comme une durabilité accrue ou une résistance chimique.
Matériaux utilisés dans la co-extrusion
La co-extrusion implique le traitement d'une grande variété de matériaux thermoplastiques, chacun choisi pour ses propriétés spécifiques qui contribuent au produit final. Voici quelques-uns des matériaux les plus importants utilisés dans la co-extrusion :
-
PVC (Polychlorure de vinyle) :
L'un des thermoplastiques les plus polyvalents et largement utilisés dans la co-extrusion. Le PVC est apprécié pour sa durabilité, sa résistance chimique et son rapport qualité-prix. Il est couramment utilisé dans les tuyaux, les tubes médicaux et les profilés pour l'industrie de la construction.
-
PE (Polyéthylène) :
Le PE est reconnu pour sa flexibilité, sa résistance aux chocs et ses propriétés de barrière contre l'humidité, ce qui le rend idéal pour des applications telles que les films d'emballage, les tubes et les revêtements de câbles. Il est souvent co-extrudé avec d'autres matériaux pour améliorer la résistance à l'humidité.
-
PP (Polypropylène) :
Avec un bon équilibre entre rigidité, résistance et résistance chimique, le PP est fréquemment utilisé dans les pièces automobiles, les dispositifs médicaux et les emballages. Sa stabilité thermique en fait un choix populaire pour les produits exposés à des températures élevées.
-
PC (Polycarbonate) :
Le polycarbonate est apprécié pour sa résistance aux chocs et sa transparence, ce qui le rend idéal pour des applications nécessitant une dureté et une clarté optique. Il est couramment utilisé dans la production de profilés techniques, de panneaux et de feuilles pour des composants de construction et électroniques.
-
PA (Polyamide ou Nylon) :
La polyamide offre une grande résistance mécanique et une résistance à l'usure, ce qui en fait un choix idéal pour les pièces automobiles, les engrenages et les applications industrielles. Elle présente également une excellente résistance à l'abrasion et aux produits chimiques, ce qui la rend précieuse dans les profilés techniques et les tubes.
-
PMMA (Polyméthacrylate de méthyle) :
Connu pour sa clarté et sa résistance aux rayures, le PMMA est souvent utilisé comme alternative au verre. Ses propriétés optiques en font un matériau idéal pour les lentilles, les couvertures d’éclairage et les feuilles transparentes.
-
PEEK (Polyéther éther cétone) :
Le PEEK est un thermoplastique haute performance utilisé dans des applications exigeantes en raison de ses propriétés mécaniques exceptionnelles, sa résistance chimique et sa tolérance à la chaleur. Il est couramment utilisé dans les industries aérospatiale, automobile et médicale, notamment pour les composants nécessitant résistance et durabilité dans des conditions extrêmes.
-
FEP (Fluorure d'éthylène propylène) :
Le FEP offre d'excellentes propriétés antiadhésives et une résistance chimique, et est souvent utilisé dans les revêtements, les tubes et l'isolation des câbles. Sa capacité à maintenir ses performances sur une large gamme de températures le rend idéal pour les environnements difficiles.
Chaque matériau peut être stratégiquement placé dans une couche spécifique lors de la co-extrusion pour optimiser les performances du produit final, que ce soit pour la résistance mécanique, l'isolation ou la qualité esthétique. En exploitant les propriétés de ces matériaux, les fabricants peuvent créer des produits avancés et multifonctionnels adaptés à une large gamme d'industries.
Solution de co-extrusion de Bausano
Bausano propose une gamme complète de co-extrudeuses utilisées dans des industries telles que la médecine, la recherche et la fabrication de plastiques. Nos co-extrudeuses sont capables de traiter une large gamme de matériaux thermoplastiques et sont utilisées pour produire des tubes médicaux, des tubes multilumen, des tubes co-extrudés, des profilés techniques, des plaques, des feuilles et des bandes colorées co-extrudées sur des tubes, des câbles et des profilés. L'accent mis par Bausano sur le contrôle de la viscosité des polymères garantit des produits de haute qualité et minimise les problèmes liés à l'instabilité des interfaces et à l'incompatibilité des matériaux.